PVD jewelry is changing how we wear and enjoy accessories. Using physical vapor deposition, this high-tech coating makes jewelry more durable, vibrant, and waterproof. In this guide, we’ll explain how PVD works, why it outperforms traditional plating, and how it brings both beauty and long-lasting quality to your collection.
1. What Is PVD jewelry?
PVD jewelry refers to jewelry that undergoes surface treatment using PVD technology, which in turn gives the jewelry stronger surface performance and a more refined appearance. Because of these qualities, it is often also called waterproof jewelry.
Specifically, PVD, or Physical Vapor Deposition, is a high-tech process that takes place in a vacuum chamber. Solid metals—like titanium, gold, or zirconium—are vaporized and then deposited atom by atom onto the surface of an item. As a result, an ultra-thin coating (as little as 0.1 to 5 microns thick) forms that’s extremely durable, corrosion-resistant, and visually striking.
2. The Technical Principles of PVD Jewelry
2.1 4 Essential Steps
- Creating a Vacuum
The object to be coated is placed in a sealed chamber, which is then vacuumed down to a near-zero pressure. The process ensures a clean environment free of air and moisture. - Activating the Material (Target)
Heat or ion bombardment transforms the coating material, such as titanium, into a gas. In sputtering methods, high-energy argon ions slam into the target material, dislodging its atoms. - Transporting the Vapor
The vaporized atoms float freely in the vacuum or plasma and settle evenly over the jewelry surface—like an invisible atomic rainfall. - Condensing and layering
These atoms form a dense and tightly bonded coating. By adjusting parameters like temperature and voltage, manufacturers can customize the layer’s structure and appearance.
2.2 Technical Key Points
- The importance of vacuum: Avoid reactions between oxygen, water vapor, and the coating to ensure purity and uniformity.
- Energy control: The evaporation of the target material requires precise temperature or ion energy, for example, in sputtering, the energy of argon ions needs to reach 10-100 electron volts.
- Substrate pretreatment: The jewelry surface undergoes ultrasonic cleaning and plasma etching. These steps remove grease and oxidation and improve coating adhesion.
3. Three Main Types of PVD
3.1 Thermal Evaporation
- Principle: Directly heating the target material until it vaporizes and then naturally condensing. Electron beam evaporation (EB-PVD) uses a focused electron beam to provide localized heating. This method processes refractory metals like tungsten, which melts at 3422°C.
- Process variant: The multi-arc evaporation technique generates metal plasma through arc discharge, achieving a deposition rate of up to 1 micron per minute.
- Pros and cons: The equipment is simple, but the coating uniformity is poor; it is often used for optical lenses or low-precision decorative items.
3.2 Magnetron Sputtering
- Principle: Argon ion bombardment targets the surface and “blows off” target atoms via momentum transfer. Magnetron Sputtering technology uses an annular magnetic field to trap electrons. This process creates a high-density plasma and increases deposition efficiency over three times.
- Technical advancement: High-power pulsed magnetron sputtering (HiPIMS) uses microsecond high-voltage pulses with power up to 1000 kW. This procedure raises ion energy beyond 200 eV. The coating density approaches the theoretical maximum. For example, a Swiss watch brand uses HiPIMS to apply diamond-like carbon (DLC) coatings. The friction coefficient reaches as low as 0.1, similar to lubricating oil.
- Application scenario: suitable for large-area uniform coating, such as low-radiation architectural glass or a black matte coating on a smartwatch frame.
3.3 Ion Plating
- Composite technology: By using both sputtering and evaporation, a negative voltage (−500 to −1000 V) is applied to the surface of the substrate, which pulls in high-energy ions to hit the coating, creating a strong nanostructure.
- Performance advantages: Adhesion is improved by 50% compared to traditional processes, allowing for perfect coating of complex shapes (such as hollow rings or gemstone-inlaid bases).
- Microscopic structure control: By alternately depositing TiN and Al₂O₃ nanolayers (each layer 5–10 nanometers thick), the coating hardness exceeds 5000 HV while also possessing crack propagation resistance.
4. Functions of PVD Technology
As early as 1857, Faraday’s experiment on vacuum metal evaporation revealed the embryonic form of PVD. However, with the development of theory and the improvement of practice, PVD technology has also been applied in various industries.
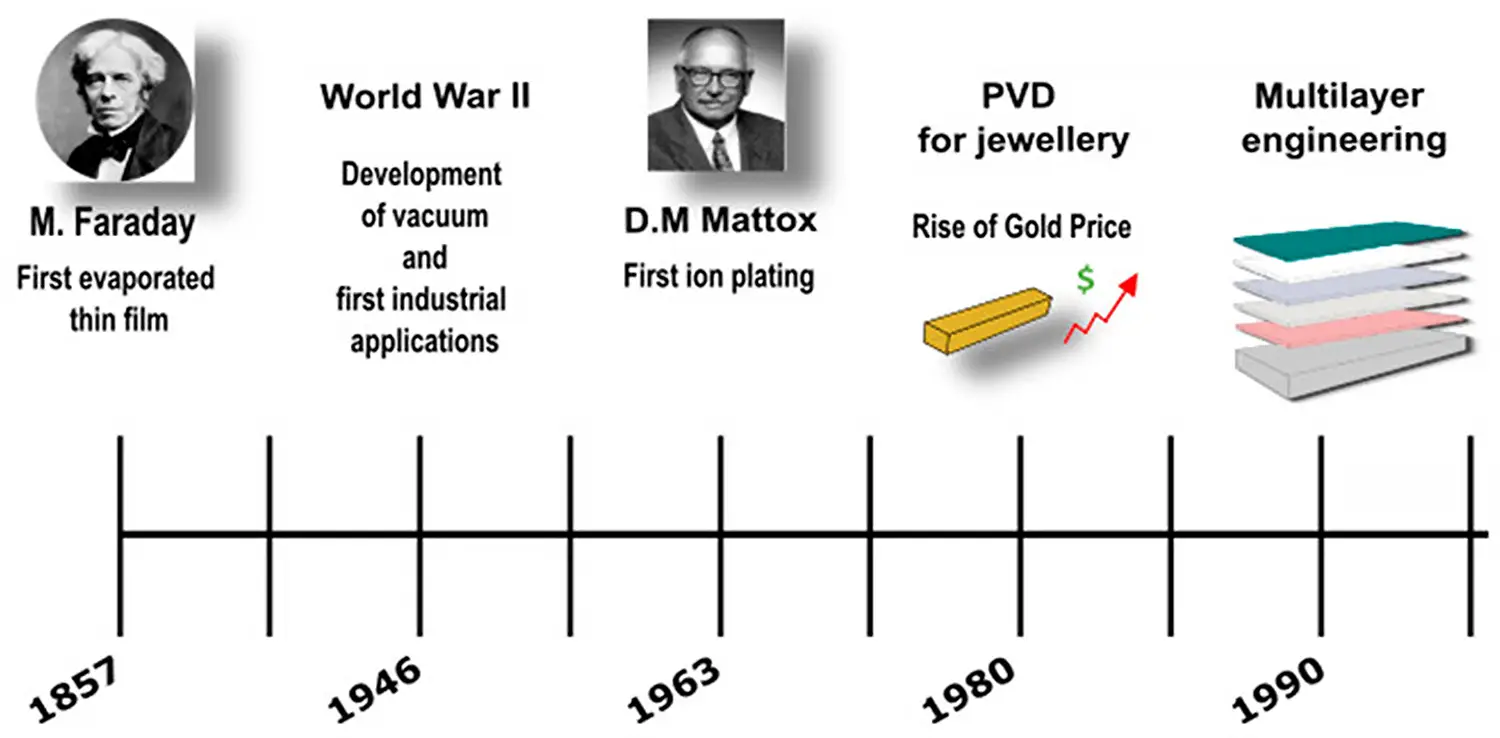
Surface Treatment
PVD makes surfaces harder, more resistant to wear, and longer-lasting by adding thin layers like titanium nitride (TiN), chromium nitride (CrN), or diamond-like carbon (DLC). Consequently, it is used in aerospace, cutting tools, and medical implants. In addition, the PVD coatings protect against corrosion from moisture and chemicals, which benefits parts used in the marine, automotive, and oil and gas industries.
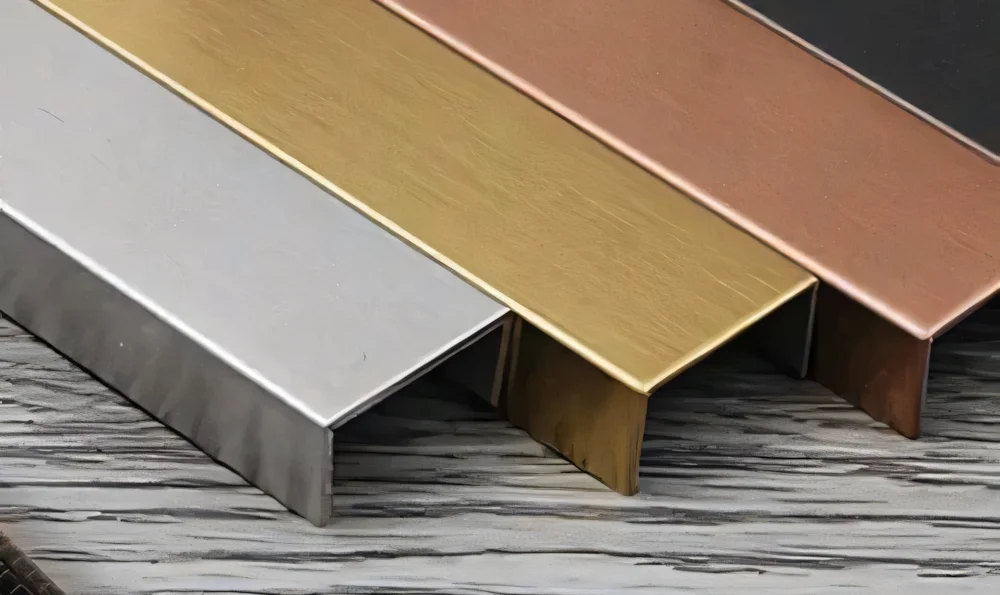
Thin Film Deposition
PVD deposits functional thin films onto substrates. For example, indium tin oxide (ITO) coatings are conductive and transparent, ideal for displays, solar cells, and touchscreens.
PVD also forms barrier layers that block moisture and gases, protecting packaged food, medicine, and sensitive products and extending shelf life.
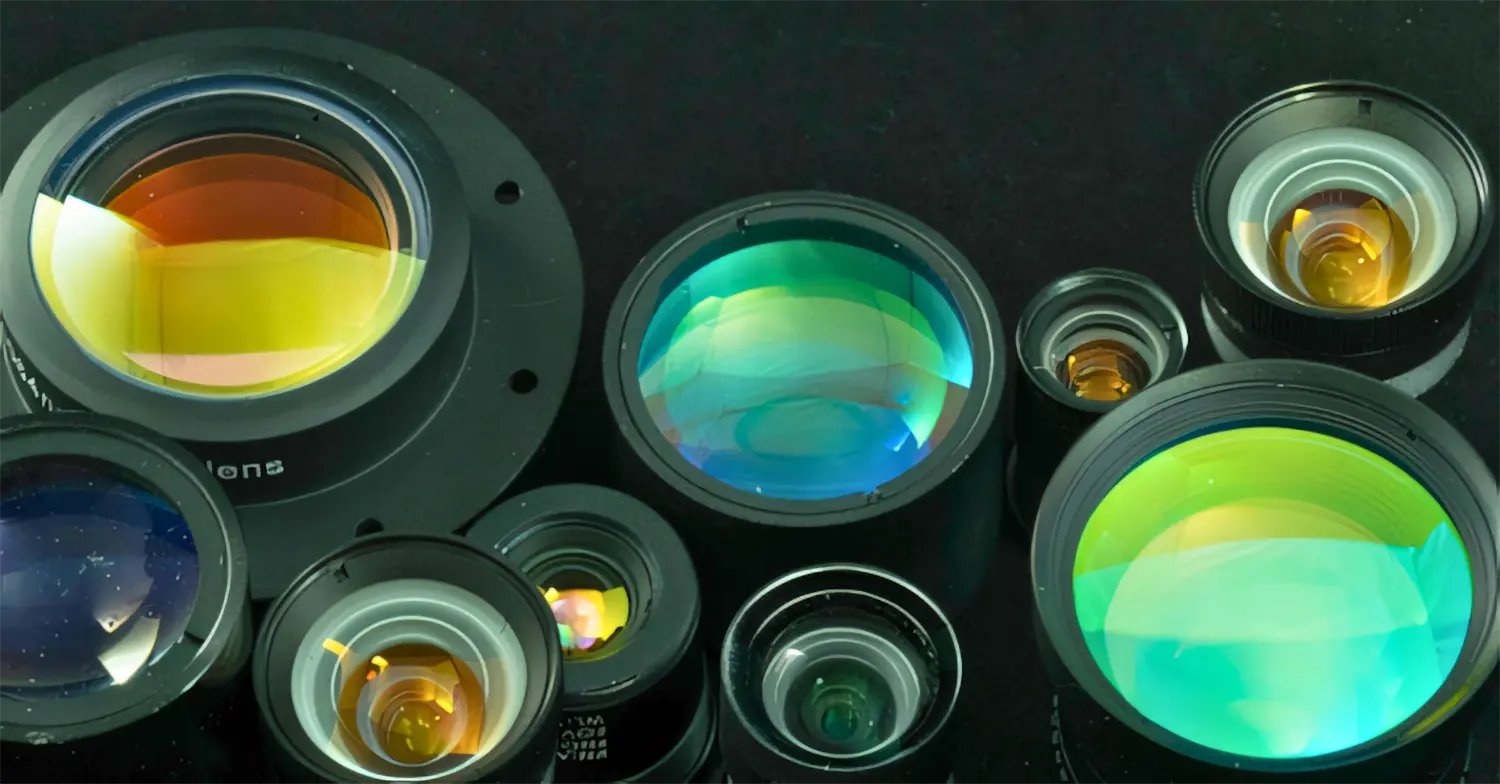
Aesthetic Applications
PVD allows metal films like gold, silver, or titanium to be applied on surfaces for custom finishes. Jewelry, watches, and electronics gain scratch-resistant, luxurious coatings.

5. PVD Jewelry vs. Traditional Electroplating Jewelry
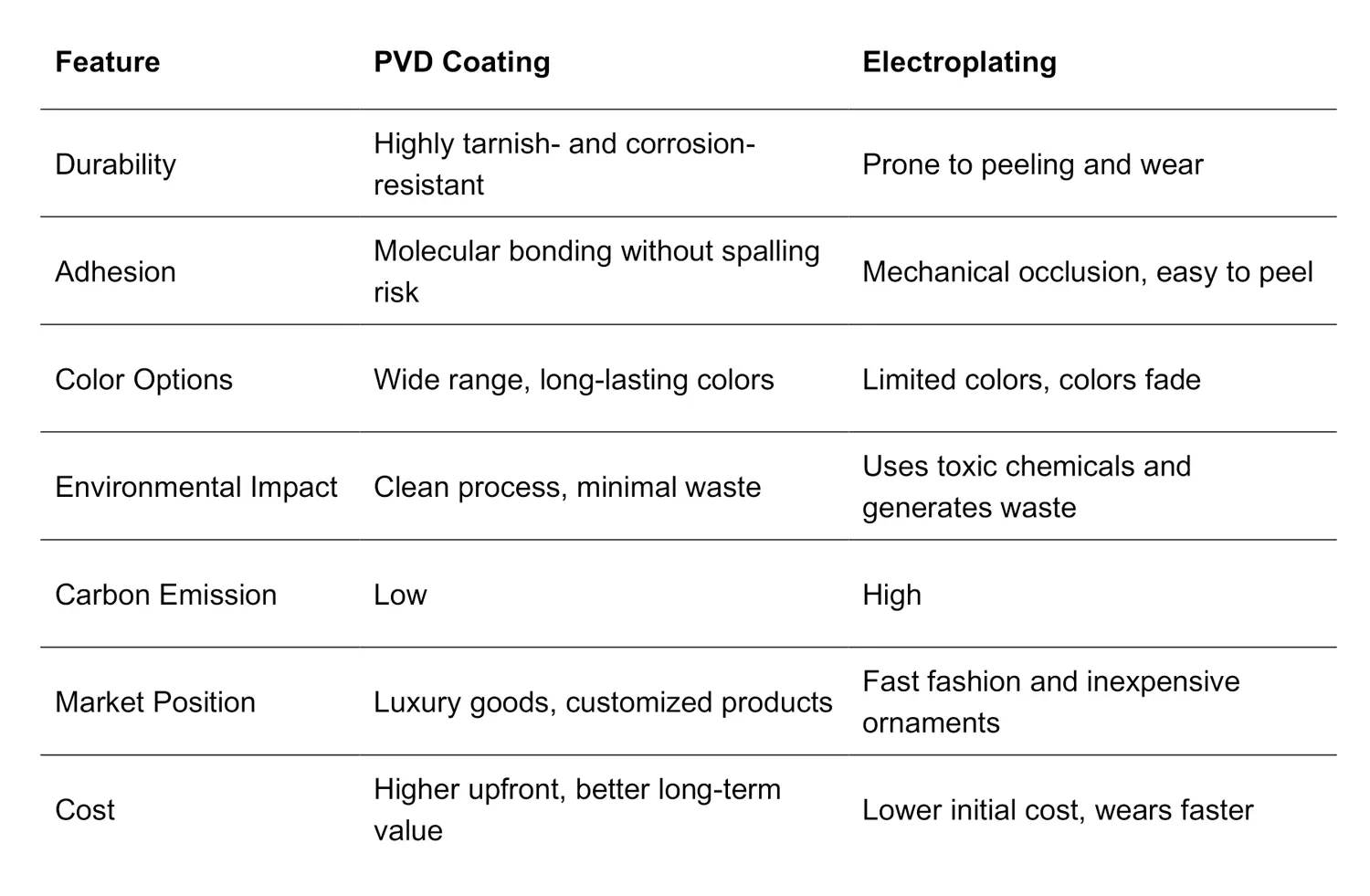
5.1 Durability
Electroplated coatings are typically thin and have low adhesion, so under friction or chemical erosion, they are likely to peel off. On the other hand, PVD coatings have better wear and corrosion resistance and stronger adhesion thanks to the application of physical vapor deposition techniques.
5.2 Environmental Impact
Electroplating technology requires the use of a large number of chemicals, and the resulting wastewater and waste gas pose a threat to the environment and the health of workers. For example, for every 1 kg of gold-plated ornaments, 50 liters of cyanide-containing wastewater and 3 kg of heavy metal sludge are needed.
In contrast, PVD technology doesn’t use harmful chemicals and creates very little wastewater. Moreover, 95% of argon is reused, and over 70% of the target material is utilized (compared to only 40% in electroplating). As a result, PVD cuts the overall carbon footprint by about 70% compared to electroplating. Therefore, PVD is a more environmentally friendly coating technology.
5.3 Color Options
Electroplating technology typically limits the color range, making it susceptible to fading. PVD technology can provide a greater variety of color choices, and these colors are more lasting and can maintain the luster of jewelry for a long time.
5.4 Cost
Electroplating technology equipment is simple and cost-effective, making it suitable for mass production. PVD technology equipment is more complex and requires a higher initial investment, but due to the durability and environmental friendliness of its coatings, PVD technology has a higher cost-performance ratio in the long run.
6. Characteristics of PVD Jewelry
- Rich Color Selection: Colors include gold, rose gold, silver, gray, black, and gradient, with stable finishes that last.
- Improved Durability: PVD coating can improve the wear resistance and corrosion resistance of ornaments. In the corrosion resistance test, the PVD coating was free from corrosion in 5% salt spray for 200 hours, far exceeding the 50-hour limit of electroplating. It can sustain its original shine and hue for an extended period.
- Personalization: Uniform, stable coatings allow for varied colors and textures to meet fashion demands.
- Material Compatibility: It is compatible with stainless steel, titanium, ceramics, and treated plastics, allowing for lightweight designs.
- Eco-Friendly: It avoids the toxic chemicals and wastewater typical of plating, thereby meeting modern environmental standards.
7. The Future of PVD
- Low-temperature PVD allows coating on plastics and resins.
- Nano-layered films combine TiN and Al₂O₃ for hardness beyond 5000 HV and crack resistance.
- HiPIMS achieves ultra-dense coatings with ion energies up to 200 eV.
- Recycling-friendly coatings improve resource use.
- As technology advances, costs will drop, expanding applications.
- The PVD market is growing rapidly, especially in high-end jewelry.
8. How to Choose and Care for PVD Jewelry
8.1 PVD Jewelry Buying Tips
- Basic materials: We recommend selecting stainless steel or titanium alloy. These materials balance strength, safety, low allergenicity, and waterproof characteristics.
- Craftsmanship identification: High-quality PVD coatings have no accumulation at the edges, and the color is uniform at the corners.
- Brand assurance: Different brands have varying quality of PVD jewelry due to differences in production equipment, processes, and materials. It is best to choose a trusted brand and check buyer reviews and after-sales guarantee policies.
8.2 Cleaning & Storage
- Clean: Use clean water, mild soapy water, or a jewelry cleaning solution. However, do not use cleaning agents containing ammonia, chlorine, or other irritating substances. Additionally, wipe with a soft cloth rather than a polishing cloth or any other hard fabric.
- Storage: First, clean and dry the jewelry thoroughly. Then, seal it in a plastic bag or store it in a soft storage pouch or jewelry box to protect it from light. Additionally, pack different pieces separately to prevent friction and scratches.
8.3 Daily Wear Tips for PVD Jewelry
- Remove jewelry during intense activities to prevent damage to it and hurting yourself.
- Avoid rubbing against hard surfaces.
- Apply lotions or sunscreen before wearing, not after.
- Rinse jewelry after swimming or sweating.
- Regular cleaning not only prolongs the life of the coating but also helps maintain the gloss of the jewelry surface. This is important because the surface can sometimes appear dull due to stains, sweat, dust, cosmetics, sunscreen, and other factors, rather than actual discoloration of the coating.
8.4 PVD Jewelry Lifespan
This long-lasting jewelry usually has a service life of 2–4 years, depending on the wearer’s environment as well as the level of cleaning and maintenance. If your purchase store offers a warranty and meets the after-sales conditions, your jewelry can last even longer. Therefore, it is important to understand the relevant after-sales policies before buying.
9. Conclusion: The Beauty of Lasting Innovation
The above is Domyee’s interpretation of PVD technology. As technology continues to evolve, the article will also be updated regularly. If you find it useful, feel free to bookmark and share it. If you have other questions, feel free to check the FAQ page for answers.
Subscribe to Domyee to continuously receive more intriguing industry knowledge and discount information.
Thank you for reading.